Solving the Encoder Problem
Written on February 1st , 2020 by Emily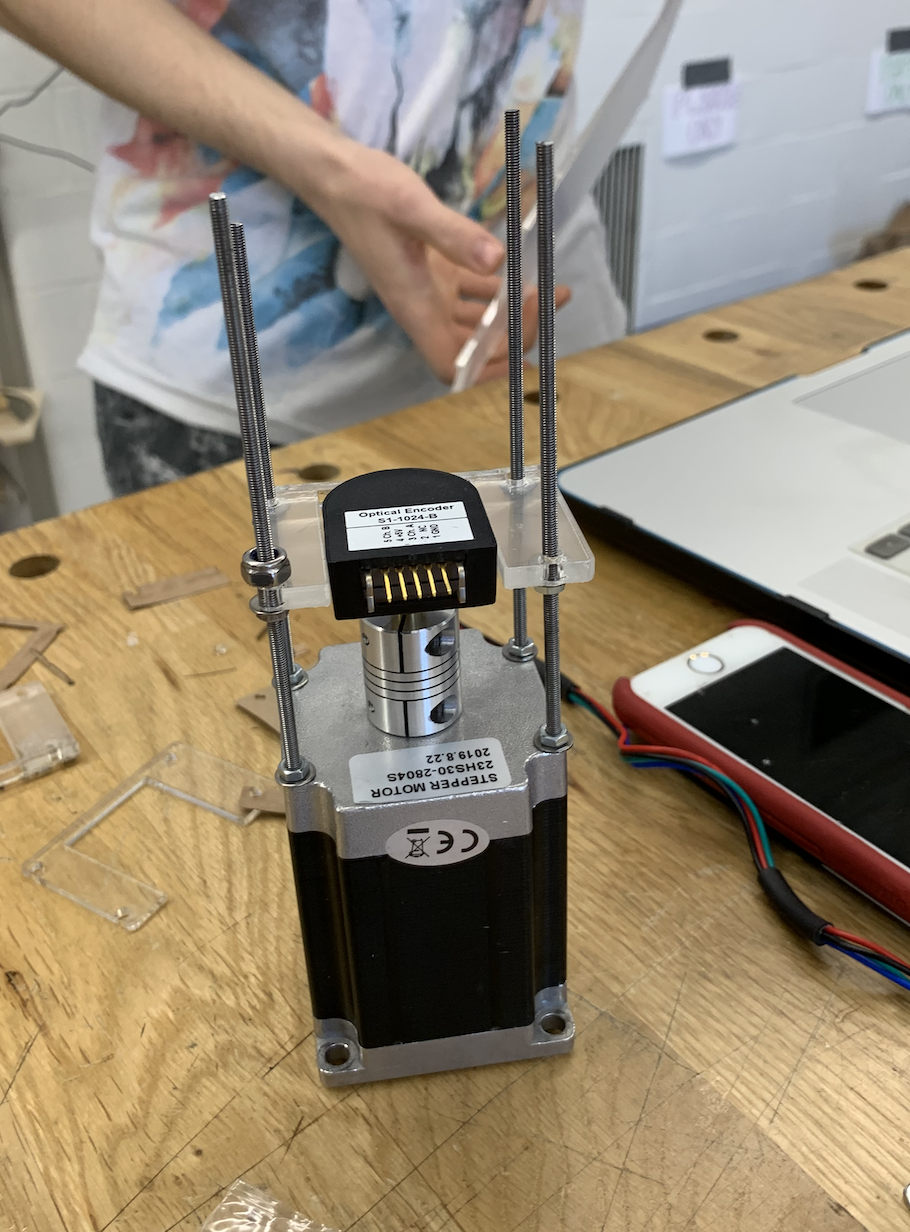
Checking the Final Fit of the Backshaft, Coupler, Encoder, and Mount
The electro-mechnical team moved quickly through January in order to have a complete first prototype to hand off to the software team so they could start working on the controls and vision. After handing off the first prototype, we quickly realized we were going to need to add motor encoders to our system as any slight bump to the platform would cause us to lose our calibrated position. The issue was that we hadn’t ordered motors with back shafts and the delta arms take up the entire front shaft so it seemed like there would be no way to attach encoders!
We consulted with Jonathan Spike from the Wat-I-Make team and he provided us with a set of encoders to use and then we worked together to make a plan to attach them. We realized the back of the motors had a small, approximately 2mm slot that rotated with the shaft. This seemed like a good place to start.
We went to the E5 Student machine shop to see if we could use the lathe to design a press-fit shaft that could be installed into the back of the shaft. After a lot of trial and error, we eventually found dimensions that could be securely and repeatably installed. From there it was easy to order shaft couplers to attach the encoder to the back shaft and then we laser cut an acrylic mount that braced the encoder body against the shaft.
The final result is a reliable encoder that allows us to have more robust motor position tracking!